Как болты DIN 933 выдерживают экстремальные нагрузки: испытания на прочность
Болт — простая, но невероятно важная деталь. Именно он держит конструкции, технику, мосты и даже космические корабли. Но насколько прочны болты, которые мы используем каждый день? Сегодня разберем, какие испытания проходят болты DIN 933 и могут ли они выстоять в экстремальных условиях.
Из чего сделаны болты и почему это важно?
Материал играет ключевую роль в надежности болта. Большинство болтов DIN 933 изготавливаются из углеродистой или нержавеющей стали. Первые — дешевле, но подвержены коррозии, вторые — дороже, но не ржавеют. Также встречаются болты из титана, алюминия и даже суперсплавов для авиации.
Кстати, если вам нужно болт DIN 933 купить, обращайте внимание не только на размер, но и на класс прочности. Он указан на головке болта (например, 8.8 или 10.9). Чем выше число, тем выше предел прочности.
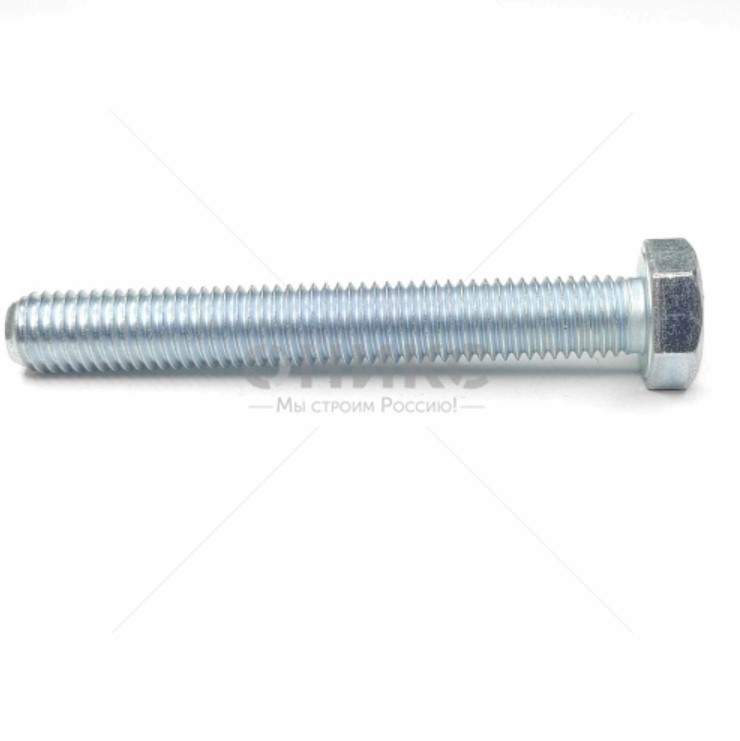
Какие испытания проходят болты?
Болты DIN 933 тестируют на нескольких уровнях. Давайте разберем основные виды испытаний:
1. Испытание на растяжение
Это базовый тест, который показывает, выдержит ли болт нагрузку без разрушения. Болт фиксируют в гидравлическом прессе и начинают растягивать с увеличением усилия. Если болт рвется раньше расчетного значения, значит, его нельзя использовать в ответственных конструкциях.
2. Испытание на срез
В реальных условиях болты редко испытывают только растяжение. Чаще они подвергаются нагрузке на срез — например, в соединениях, где детали движутся относительно друг друга. В лаборатории болт зажимают между двумя пластинами и нагружают боковым давлением, проверяя, при каком усилии он сломается.
3. Ударная вязкость
Этот тест особенно важен для болтов, работающих в низких температурах. Чем ниже температура, тем хрупче становится металл. Испытание проводят в камере с жидким азотом при -40°C, после чего болт подвергают ударной нагрузке.
4. Тест на коррозию
Болты, особенно оцинкованные, проверяют в «соляном тумане». Их помещают в камеру с влажной соленой средой и оставляют на 24–72 часа. Если за это время появляются очаги ржавчины, значит, покрытие недостаточно надежное.
5. Вибрационные тесты
Этот тест актуален для болтов, используемых в автомобилях, строительстве и промышленности. Их закрепляют на платформе, которая имитирует длительную вибрацию, и проверяют, не ослабляется ли соединение.
Где применяются болты с высокой прочностью?
Болты, выдержавшие все испытания, используют в самых ответственных местах:
- Мосты и эстакады – они работают под постоянной динамической нагрузкой.
- Авиация и космос – например, болты с титановым покрытием стоят в двигателях самолетов.
- Гоночные автомобили – там важны как прочность, так и легкость.
- Промышленные станки – высокая вибрация требует качественного крепежа.
- Нефтегазовая отрасль – болты работают в агрессивных средах, где коррозия — главный враг.
Как выбрать надежный болт?
При выборе крепежа стоит учитывать:
- Класс прочности – чем выше, тем лучше для ответственных соединений.
- Материал – оцинкованная сталь для влажных условий, нержавейка для агрессивной среды.
- Производитель – не все болты одинаково надежны, выбирайте проверенные бренды.
- Область применения – для дома подойдут стандартные болты, для авто и промышленности — с повышенной прочностью.
Итог
Болты DIN 933 — это не просто куски металла с резьбой. Они проходят серьезные испытания на прочность, коррозию и вибрации, прежде чем попасть в производство. Если вам нужен крепеж, который выдержит любые нагрузки, обращайте внимание на материал, класс прочности и производителя. Ведь хороший болт — залог надежности всей конструкции!
Источники:
- ГОСТ 7798-70, ГОСТ 7805-70 – технические характеристики болтов.
- Доклады NASA о крепежных соединениях в аэрокосмической отрасли.
- Тесты на коррозию ASTM B117 – мировой стандарт проверки покрытий.
- Технические спецификации производителей крепежа, например, Würth, Nord-Lock.